Understanding the Complexity of Modern Truck Electrical Systems
Created October 17, 2017
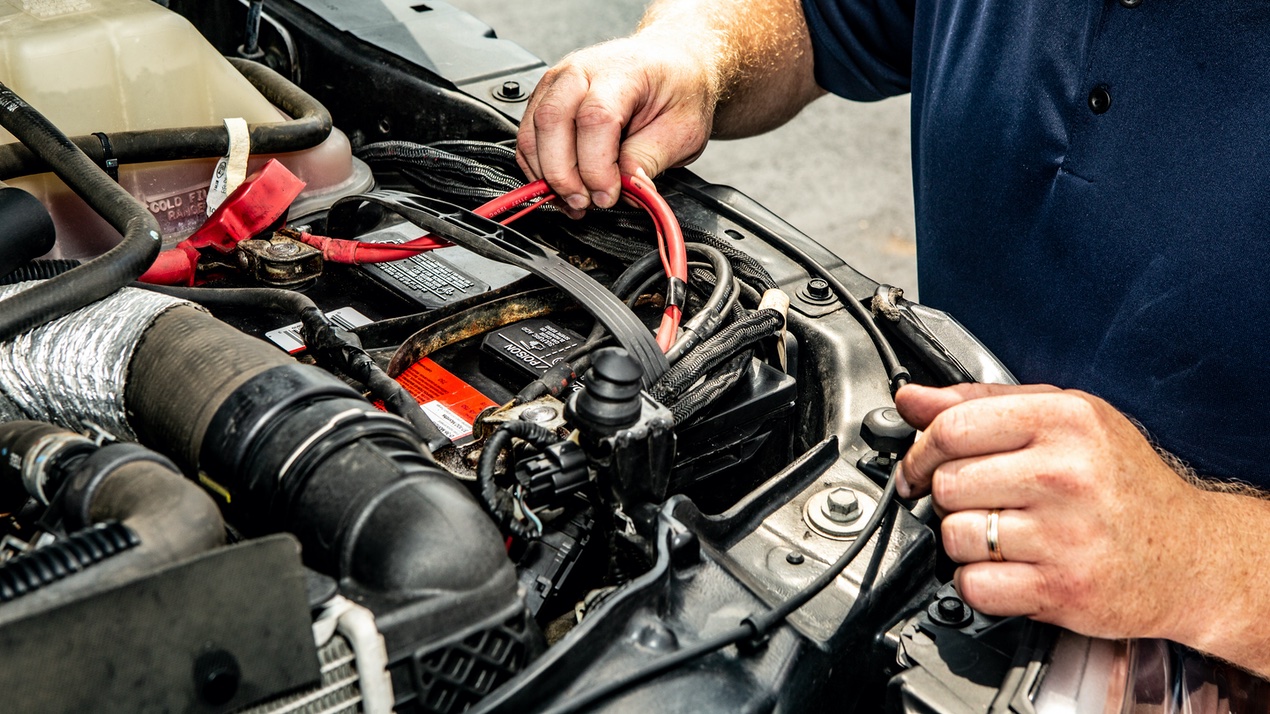
If it’s more modern, it should be simpler, right? Not necessarily. Anyone who has installed a snowplow or a spreader on a more modern work truck knows the feeling. It’s that confusing moment when you open the hood to confront an engine compartment that looks more like something from Microsoft than GM. Complex electrical systems aren’t just an issue for installers though.
Every truck these days, every trim level and option, creates a unique set of challenges for anyone trying to design any kind of powered attachment. Each truck manufacturer is slightly different (adding to the fun) but, in general, this is how they work.
Is That a Truck With a Computer or a Computer With a Truck?
These days, every truck at every trim and option level has a group of onboard computers whose job is to monitor the truck’s “health” and every aspect of its operation. Even without fancy GPS, camera and Bluetooth systems, a stripped-down truck has sensors and computers controlling fuel mix, engine temperature, emissions, electrical load, and more.
Every vehicle today comes from the factory with a keen sense of its own limits. The on-board computer monitoring system that monitors the vehicle has a series of lookup tables where it compares the sensor outputs from moment to moment. If the temperature in the engine reaches a certain point, the computer will alert the operator. If a door is ajar, an icon on the dash will inform the driver not only that the vehicle is not secure, but which door is open.
The entire setup of the various small computers and sensors throughout the vehicle is called the Controller Area Network, or the CAN. Historically, as the number of items and conditions monitored and controlled grew, direct analog wiring became difficult and then impossible. Eventually they were replaced with a highly specific kind of computer network.
There are a number of reasons for the increased complexity. Fuel efficiency drives the need to monitor inputs and outputs, continually adjusting fuel mix and airflow. Safety and reliability demand that sophisticated brake sensors continually monitor the status and functioning of each individual brake, applying or reducing friction as needed to ensure smooth, reliable and risk-free operation. And every one of the modern conveniences of a truck requires a computer. They control the preset seat and mirror adjustments that the vehicle will remember. They are responsible for every aspect of your comfort in the cab.
Not to mention, ever-changing government regulations on fuel efficiency and safety push manufacturers to innovate while also maintaining the performance that customers expect.
This, of course, all comes at a cost. In replacing miles of direct wiring and hideously complicated wiring harnesses, trucks now possess very complex programming.
The Bus Is Full
Preinstalled parts are hard enough to keep track of, and third party equipment adds to the mess. Lift gates, winches, spreaders, and snowplows all place a burden on the systems of the truck. Because there are dozens of attachments from a multitude of suppliers, the automotive manufacturers have determined that they cannot account for all the potential combinations.
The network of computers, sensors and wiring (the infrastructure of the CAN) is known as the CAN bus, and only certain things are allowed on the “bus.” Snowplows and their systems typically aren’t supported by the CAN bus infrastructure.
The Struggle Continues
This obviously poses a problem for snowplow and spreader manufacturers. Because the plow systems aren’t part of the CAN bus, any changes the plow makes to the vehicle will look like problems to the system, instead of additions.
For example, during the initial activation of a snowplow, there is a voltage “inrush” peaking for several milliseconds at a level higher than the pump operates at normally. That voltage comes directly from the truck and is (very temporarily) lost from the truck’s energy “budget,” leading the truck’s system to think there’s a problem.
Remember how the truck’s CAN has lookup tables outlining potential problems and that anything the plow is doing is invisible to the CAN as a desired function? If the voltage “inrush” spikes high enough, for a long enough period of time, the computer will record it as a fault, or a problem in the system.
Working and Playing Nicely With Others
As a result, work-truck attachment manufacturers work with truck manufacturers to understand the limits and boundaries of equipment. They modify their hardware, not so that it can talk to the CAN bus, but so that it doesn’t exceed the limitations.
For example, there are additions that can be made to plow circuitry that slow down and level off the “inrush” voltage, so that it remains below the level that will cause problems.
As truck trim levels increase, the number of items drawing on the total amount of energy on the truck grows. As a result, snow-plow manufacturers look for ways to do their jobs with as little energy as possible.
The Good News
Ultimately, the plow manufacturer is responsible for integrating the plow with the existing truck electrical system, not the other way around. Thus, it can take time to add plows to new truck platforms, especially if that platform is brand new.
As a result, more than any other factor, truck electrical systems can easily keep a truck off a plow’s approved list for some time.
The good news is that once plow manufacturers put a plow on a new-truck approved list, you can be sure that it is safe and ready to provide optimum performance.
To learn more about which plows fit best on your truck, use our Quick Match feature or visit your local dealer.